Connecting...
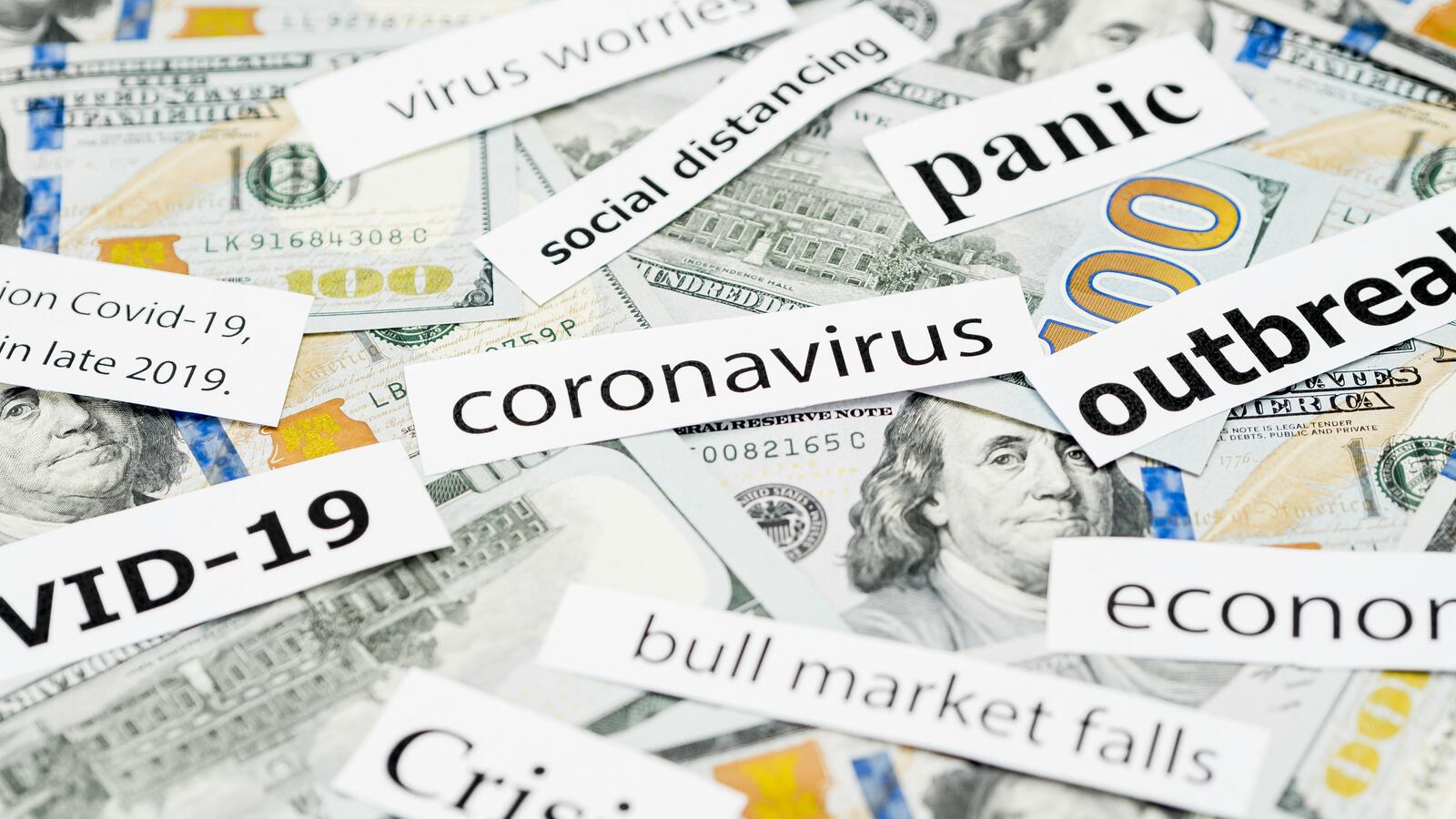
How COVID Identified a Weakness of Just-In-Time
For decades, Just-In-Time (developed by Toyota’s Taiichi Ohno) has been seen as the best way to run a manufacturing operation. Just-In-Time, in its simplest explanation, allows companies to reduce the amount of inventory they are holding which in turn reduces the amount of capital invested in inventory.
Although this system doesn’t work for every manufacturing operation, generally this has worked extremely well in ensuring production doesn’t get interrupted in any situation.
This all changed when COVID hit the world.
We all know what happened, and is still happening in many countries. All stages in the supply chain of every industry were affected. Whether it was the farmer not being able to get their produce to the producer, or the factories not being able to get raw materials to produce their products.
Factories that were not holding enough inventory or parts or raw materials, found themselves not able to replenish their inventory and had to stop the production lines. This resulted in shortages of many products around the world and there was virtually no one around the world who wasn’t impacted by either rising prices or essential items not being available.
While it still makes sense, where possible to keep inventory levels low and follow the Just-In-Time methodology for manufacturing sites. However, businesses are now realizing that they have to increase inventory levels to be better prepared for possible interruptions in the supply chain.
How much inventory companies need to keep on hand is up to each company's analysts to plan for based on the potential risks their business has, the length of their supply chain, etc. However, businesses need to be more aware of the potential impacts this weakness has shown all of those in the manufacturing space.